Here it is…
The last step of my wood finishing troubleshooting “cheat sheet.”
Next week we’ll move on to brand new tips and topics.
For now, let’s conclude this series with Step 5: Water and Chemical Resistance of the Finished Piece.
Yes, this is related to last week’s tips on “drying and curing,” and falls into lockstep with the conversation you should have with your customers (or yourself, for DIYers) about how to use and care for the finished piece once it is installed or delivered.
Conversation One: How to safely use a newly finished piece that is not fully cured.
Let’s face it, some jobs get rushed into delivery and the finish you just applied a day or two ago has not had the chance to fully cure – I hear this all the time.
Therefore, after delivery or installation, you should advise your customers to take extra care in the daily use of their new wood finish.
If it’s a tabletop or countertop, they need to avoid leaving wet drinking glasses or hot containers on it. Advise them to use platers, coasters or a tablecloth to protect the finish while it goes through the final cure cycle, which can take between 7 and 10 days.
To be on the safer side amid so many climate and human variables, I would tell customers, “coasters or tablecloths only” for 10 to 14 days.
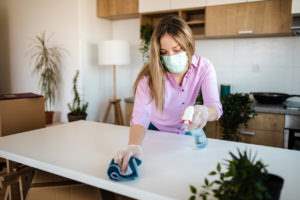
Conversation Two: How to clean and protect the new finish.
Using the right products for daily cleaning is important – we do not want to damage the finish with harsh cleaning chemicals.
During curing, advise your customers that the best way to clean the surface is with a soft sponge lightly dampened with water, immediately followed by a gentle buffing with a soft cotton cloth that absorbs water and does not leave micro-scratches.
Once the finish is fully cured and has reached its maximum chemical resistance, you can then advise on the use of stronger household cleaners.
It’s best to consult with the finish manufacturer on exactly what type of cleaner to use, but my go-to has always been ready-to-use glass cleaner.
If the customer wants to disinfect the surface (now more common than ever) I strongly suggest a neutral pH (neutral is 7.0) disinfectant diluted to the correct level to ensure proper sanitizing and disinfecting. Your local janitorial supplier can help you select the right product for this task.
Any disinfectant with a high pH (above 8.5) may dull or slowly strip the finish. Again, consult with your supplier.
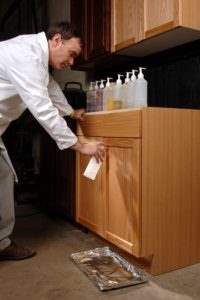
Conversation Three: What to expect from the new finish.
Not all wood finishes are alike. Due to the wide array of resins used to make water-based coatings, we see an equally wide range of performance qualities regarding how the finishes handle different types of foods and chemicals.
For example, different wood coating formulas have various resistances to vinegar, citrus juices, ketchup, coffee, cooking oils and different blends of alcohols.
Your finish manufacturer is responsible in giving you the performance characteristics of each coating they make based on ASTM or KCMA testing standards.
It is best that you review the project with both the customer and the finish supplier to ensure everyone is on the same page regarding what they can expect from the finish being delivered to the jobsite.
No finish is bullet-proof, but with the correct product selection and a clear understanding of what the customer should and should not do in terms of daily maintenance and care will head-off any disputes down the road.
There’s nothing worse than “falling down at the finish line,” so I hope the above tips on water and chemical resistance were helpful to you.
And….that concludes my “Wood Finishing Troubleshooting Cheat Sheet!”
Do YOU have any troubleshooting tips of your own? Maybe some of you had to learn the hard way? (I’ve had my share of those). Please share your thoughts or read what others are saying in the comments section below.
I wanted to thank you for this series on troubleshooting. One thing that really stood out to me was your mantra of applying thin/light coats. It is something I have to constantly remind myself and probably the item that makes the biggest difference to my finishes.
Thank you, Keith.
-JW-
We recently finished a set of kitchen cabinets with three coats of EM6000 at about 3 mils per coat. I’m wondering if for durability purposes you’d recommend topcoating with a final coat of EM2000. My understanding is that it’s more durable. I’d rather not risk using the crosslinker for the final coat and risk having to sand it off if I don’t mix properly. Thanks for any tips and for all the great posts
Zach — Thank you for your inquiry. I am confident that the EM6000, when used as a stand-alone finish, will give your cabinets good protection over a long period of time. I recommend that you wipe off any grease/grim with a neutral pH cleaner to keep the finish looking healthy.
-JW-