Updated: May 2024
My earlier post about water based varnish generated some questions about water based lacquer, so I’ll address those today.
Just so you know, anywhere from three to four times a day my phone rings and a customer asks, “Does [this product] create a lacquer type finish?”
When the word “lacquer” enters the conversation a deep, wide rabbit hole opens…
And we can quickly descend into the world of defining the chemistry, function and purpose of what a “lacquer” really is.
Some conversations are quick; others seem to take forever to conclude. So, I’ll do my best to keep things simple and avoid the hair-splitting minutia.
Here are a few important points that will help you determine if the term “lacquer finish” is appropriate for your own world of wood finishing.
A Functional Definition of Lacquer
I’ve always found it best to categorize wood finishes by their function and performance. Artisan and industry standards over the long-term have helped to define the products that we use.
So, by that measure, as a wood finisher, why would you consider using a lacquer over another type of finish? Here are several answers from my customers:
• It’s user friendly from a repair and refinishing perspective, i.e. the coats/layers “burn in” to each other.
• It dries fast.
• It dries clear – or nearly clear when applied in the right ambient conditions.
• It offers protection/durability on a “utility” basis; it is a good all-purpose interior finish.
Ready for the deeper dive? Here we go…
The “Official” Definition of Lacquer
The Merriam-Webster dictionary defines lacquer as…
1a: a spirit varnish (such as shellac)
1b: any of various durable natural varnishes especially: a varnish obtained from an Asian sumac (Rhus verniciflua) — called also Japanese lacquer
2: any of various clear or colored synthetic organic coatings that typically dry to form a film by evaporation of the solvent especially: a solution of a cellulose derivative (such as nitrocellulose)
OK, there are two keywords here that gets the dust flying – varnish and shellac.
While I learned years ago never to argue with lexicographers, I do find definitions of words that veer outside of specific industrial terminology often end in bar fights.
So, with this in mind, let’s respectfully toss out the words “varnish” and “shellac,” and instead focus on nitrocellulose lacquer to help us define what has also become available in water based formats in the late 20th century going forward.
Nitrocellulose Lacquer vs. Water Based Lacquer
What is a nitrocellulose lacquer? A “nitro lacquer” is made from the fibers of cotton and cellulosic materials, which are reacted with nitric acid to create a resin.
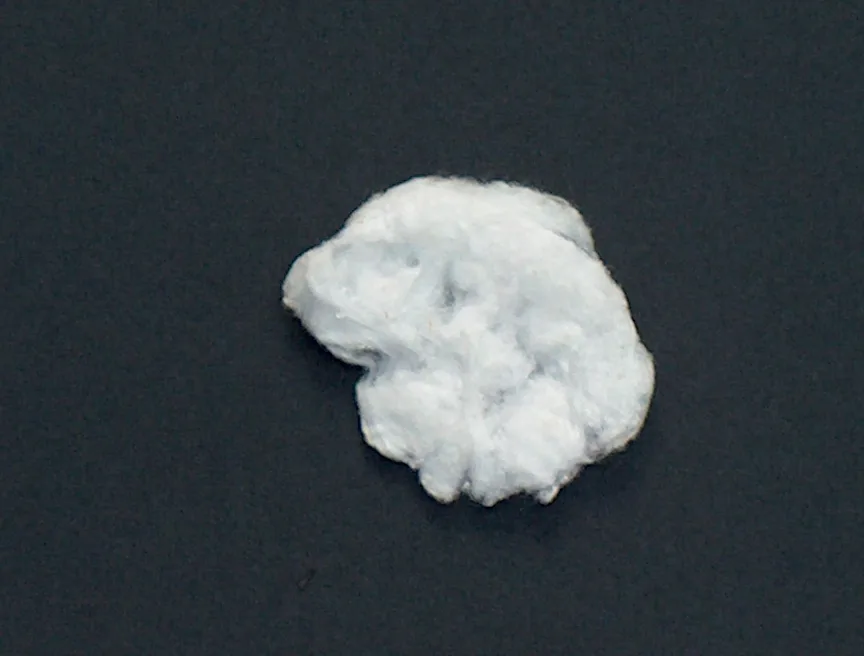
This resin, diluted with alcohols and other additives, are used to make a low-solids, highly reactive coating that found a wide array of adaptations in the early 20th century for use in furniture and automotive finishing due to their ease of use, fast dry-time and reasonable degree of durability.
The downside to nitro lacquers is the inherent danger when using them – nitrocellulose lacquers are highly combustible and require great care in their use and handling.
Skipping forward, in the early 1980’s a new array of water based acrylic and urethane resins began to make their way into wood floor coating formulas.
Because of their good durability and relative ease of use, the term “lacquer” was used when marketing these early finishes without focusing on the actual function and performance.
Thus, when I began formulating the first generation of Oxford water based lacquers, I was determined to categorize the finishes I created by how they performed compared to their solvent-based counterparts.
So, when we look at a nitro lacquer as a cross comparison, what do we see?
As I mentioned above, the very first performance value that makes solvent based lacquers so endearing to the end-user is its 100% burn-in capabilities.
“Burn-in” is the function in which the next coat of lacquer melts, or “burns” into the previous coat. Due to the very high solvent content used to make a nitro lacquer, these solvents — ketones, xylene, naphtha and other “hot” solvents — reactivate and melt the dry/cured cellulose film that they are being applied to.
This reaction allows for the cellulose resin to rewet and blend together – creating a unified, single film formation. With each coat melting into the next, the final, cured coating is easy to polish and repair.
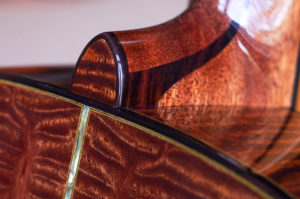
Now we find ourselves with water based acrylic coatings being sold as lacquer substitutes. Some brands available today fall short of the performance criteria to be deemed a “lacquer” the way we’re defining it – others live up to the definition quite well.
For example, the Emtech® EM6000 Production Lacquer and the refined EM7000hbl High Build Spray Lacquer provide physical characteristics and functionality that behave just like a nitrocellulose lacquer.
These characteristics are:
• 100% burn into its previously applied coat.
• Fast recoat time.
• Easy repair and polishing response.
• Good utility-grade durability.
Are these two formulas made with cellulose fiber? No, they are made with fine particle acrylic polymers and water-soluble propylene series solvents.
So, in the literal definition of “lacquer” they do not qualify. However, in their performance and function analysis they meet all the criteria of a high-quality production lacquer finish.
As you can see, this conversation can go on at length. In the end, it is up to the coating manufacturer to properly define and categorize the name and purpose of the finish they are taking to market.
By not doing this, we see on-going confusion in the wood finishing community. I hope I cleared some of it up for you today.
What water based lacquer, if any, do you use today, and what do you like/dislike about it? Please share your thoughts or read what others are saying below in the comments section.
As always, stay well and stay creative.
– Jeff
Jeff Weiss is the owner and chief chemist at Target Coatings, which has been dedicated to exclusively manufacturing water-based, low-VOC and HAPs-free wood finishes for nearly 40 years. Creator of the first water-based lacquer with 100% burn-in rivaling nitrocellulose lacquer, Jeff is considered one of the “founding fathers” of water-based technology and safety for refusing to accept the “status quo” and for refusing to expose others to chemicals he wouldn’t want to be exposed to. A U.S. Air Force veteran and former volunteer EMT, Jeff has always put service and safety first. Outside of work, Jeff is an avid fly fisherman who enjoys being immersed in and inspired by Earth’s natural beauty.
Thanks for this. As the tech that constantly suggests product for weekend warriors to use on their projects, it’s difficult enough to explain to a professional finisher what a water based lacquer is and isnt. Try explaining to the customer that bought a $59 sprayer and doesn’t understand why he cant spray real laquer. In my custom cabinet business I switched to water based finishes in ’94ish and never looked back, also have never had a call back for a finish issue. Unless it burns in to the last coat, it shouldnt be called lacquer, it should be called poly.
Sam – Thank you for sharing your view on this, and thank you for being a supporter of water-based finishes!
-JW-
Why can’t you spray true lacquer? I have finished woodwork MANY times spraying pre-cat lacquer and not waterborne finishes. My problem is now actually finding the REAL lacquers. I started a project with lacquer I bought last year and barely caught it before it went completely solid in the can, added some lacquer thinner and stirred the hell out of it and was able to use in a sprayer just fine. Just like every other lacquer finish I have ever applied, I sprayed it on with a gravity fed HVLP sprayer. If I am doing larger projects, I will use an airless sprayer. You just have to make sure that you have the correct nozzle size for what you are spraying. A gravity cup is a necessity.
Hello there. Currently we use general finishes and cambell. We also have a couple others. Cambelll is what we are currently using for our whites and it is a complete nightmare to get to the end result. I’ve got 20 years in a spray booth industrial and just took a job in a woodshop as the supervisor. I’m looking for a better water-based that will cut down the time it takes to paint a frame
Jason – Take a look at our EM6500 Pigmented Lacquer Series and the HSF5000 Primer/Surfacer. Both are excellent products.
-JW-
I had tried a number of water based finishes years ago but hadn’t used any for quite a while. As a professional cabinet maker I mostly sprayed solvent based lacquer and never found anything that matched it’s performance in the water based world. As a hobby instrument builder I don’t have access to the equipment to spray solvent based in my home shop so I adapted to french polishing with shellac on my instruments. This is a time consuming and difficult to master process which leaves a finish that while generally protective is not as robust as lacquer. Recently I began trying a few water based finishes (I figured they had probably evolved) including emtech 6000. It is far better than any of the water based finishes that I tried in the past. I am currently experimenting and testing (without sealer, with em1000 sealer, with ush3000 sealer and with 2 light coats of shellac as a sealer). All work well and produce a good finish. The real question will come down to – can it match french polish. In the world of high end classical guitars french polish is consider the gold standard of finish. The general opinion is that it can be applied thinner than any other finish and therefore have less effect on the tonal performance of the instrument. I have not seen anywhere that this has been rigorously tested either by measurement or by a blind listening (ie. take 10 high end hand made classical guitars, finish 5 with emtech 6000, french polish the other 5 and see if a blind test group can tell the difference sound wise between one and the other). This would be a great test – expensive and a fair bit of work but essentially what I’m trying to distinguish by preparing sample boards and weighing how much finish is on the board in the final finish, how thick the coating is and by measuring resonance seeing how much it effects the “tone”.
I am retired, but if I were still in the cabinet making / furniture building I would use emtech 6000 as a furniture finish without hesitation.
Thank you for your thought provoking post.
-JW-
Robert, thank you for your comments and most particularily your interest in our sealers and EM6000 lacquer which has generated quite a bit of interest among luthiers and furniture makers alike. It’ll be interesting to see how things will work out with the test you’re undertaking, so please keep us posted.
Again, thank you for writing in, and all the best to you and your work.
I think that if you’re drawing attribute-based comparisons to the solvent world then EM6000 arguably sits somewhere between conventional nitro lacquer and a precat lacquer. In my experience its burn-in capabilities are more limited than nitro because of the ~24-hour limitation, but better than the precats that I’ve used. Likewise, once cured EM6000 is less reversible/removable than nitro (though most people view this as an advantage and call it “chemical resistance”) and closer to precatalyzed lacquers. EM6000’s shelf life also fits somewhere between the two. Etc,
It seems clear to me that given the wide range of substances that were already branded as “lacquer” in the solvent world, coatings like EM6000/EM7000 don’t really stretch the term any further than it had already been taken.
I am a guitar builder who specializes in “relic” builds. Relic guitars are those made to look as if they are 50-60 years old and have been played in smokie bars and other places as such. Although I believe I probably know the answer, my question is this; Will water-based lacquer check (crack) as aged nitro does when exposed to extreme hot and cold? I can’t really produce a realistic relic guitar without having the checking process. That’s really the only reason I spray nitro. Thanks I’m advance for your answer.
Mike – I recognize the need to create a cold-check effect for relic finishes. The only way to make any of the Emtech clear coats check is to use Zinsser SealCoat at full strength under the Emtech finish. The effect will be more of a crackle look vs a cold check image. You will have to experiment with the number of coats to obtain your own procedure.
-JW-
I can’t answer your question directly, but check this out: I’ve been spraying SW Sher-Wood water based lacquer and surfacer for a while on cabinets and trim. One day, I ran out of surfacer but had an itty bit of poplar crown molding to prep. I grabbed my can of clear shellac and dabbed on a coat. Sanded, sprayed, and got a crackle by the time it was dry. Looked super cool, (if not what the client wanted and therefore had to start over).
Hi Jeff. I just bought a Sheesham wood table which was finished with an NC base lacquer. We have read reviews which said that the lacquer does not provide enough protection against water and food stains. Any recommendations on what we could use over NC base lacquer, if any? That seems to be what it was finished with. It’s a matte finish so I want to keep it that way. I was wondering about putting a water based lacquer or varish on if for some protection but I’m just not sure. Any advice is appreciated.
Thanks,
Chris D.
Chris – Thank you for your post. Many of the precat NC lacquers used in 20th Century production facilities were not of the highest quality in terms of resin solids and overall durability. If you want to refinish the existing finish you should clean/decontaminate the existing finish, then make whatever repairs are required before proceeding to a water based lacquer system. I recommend either our EM7000HBL High Build Acrylic Lacquer or our EM8000cv WB Conversion Varnish – both should be crosslinked with CL100 Crosslinker to provided long-term alcohol and high pH cleaner resistance.
-JW-
I always liked that my furniture yellowed over time. Will water borne lacquers do that? Thanks
Jim – You ask a good question. Not all water-based/waterborne coatings turn yellow or amber over time. The type of resin used in the specific WB will determine if the
coating will color shift over time. Certain types of acrylics can shift dur to the styrene content, while other acrylics remain water-white/non-yellowing. Likewise with WB urethane resins – some are aromatic hybrids that will yellow when exposed to UV and oxygen, while others remain clear. It’s comes down to how the WB formulator selects the resins and designs the coating.
I recommend that you consider our EM6000 Production Lacquer and our EM8000cv for a warm color tone similar to nitrocellulose.
-JeffW-
Hi Jeff,
I’ve been spraying SW pre cat lacquer for years. I’ve had somebody recommend Mohawks Architectural waterborne pre cat lacquer.
My question is mainly about the durability comparison, and whether the Mohawk product is still just an acrylic?
Mostly being used for cabinetry.
Thanks for any information you can give me.
Bently
Bently – Thank you for your inquiry.
I looked into the Mohawk Acrylic WB Lacquer product line and yes, it appears to be based on an acrylic resin backbone.
The type of acrylic, i.e. copolymer, styrene content, self-crosslinking, etc is not divulged, therefore I cannot offer you a cross-comparison in our Emtech line.
With this said I invite you to consider our EM6000 Production Lacquer and EM7000HBL Lacquer for your interior wood finishing applications that require a CAB-type level of durability.
-JeffW-
Hey Jeff, I’m just a carpenter/builder who does a lot of other things in the homes I build. I’ve been spraying lacquer for years with a turbine sprayer/HVLP and never had a problem. I moved to Mexico and was building there for about 10 years and everything there is lacquer as well but when I moved home to Canada, I discovered that it’s now water based and I’m having a real hard time spraying it with my equipment. The first projects went pretty so-so but now I can’t get anything to work properly. Five guns and I can only get a whisper when I need a shout. Do I need to change nozzles for better flow? I can’t clean the guns any further, I’ve filtered the paint…just stumped and the only thing I can think of is change nozzles…help? I’m all for changing to a “safer” paint but sure don’t like going through all this frustration…
Hi Bruce,
Thanks for reaching out to us with this comment. Please contact me at skline@targetcoatings.com with your gun and system type and settings. Maybe I can help you get the right adjustments made so you can spray water based finishes like you want to.
Thanks,
Seth Kline
Bruce,
Thank you for your inquiry. What type of spay equipment are you using, and what are the needle/nozzle/tips set sizes that you have available to you?
Based on your description of not getting enough fluid volume out of the various spray guns you have to work with I suspect that the tip sizes are too small.
Lastly, what type of water based finish are you working with – clear or pigmented?
-JeffW-
I have been using the EM8000 conversion varnish for the last several months and I am sold on your products.
I have sprayed solvent borne pre-cats and conversion varnishes as well as nitrocellulose lacquers in an industrial wood shop setting for many years but I have been using your product at home in my garage shop with an LVLP gravity fed gun and I have to say I am very pleased with the ease of use and durability of the finish. Even in my less than pristine spray environment I have been getting great results.
I see no need to risk health and safety when your product performs as well as a solvent system. I might add I think it performs better because it sands out so wonderfully between coats. No clogged paper means no swirlies to chase down by hand. Cleanup is a snap as well. Great stuff!
Wes,
Thanks for you comment. Always good to hear from customers who are having success with Target Coatings and Emtech finishes. Agree 100% with your assessment on not needing to risk health and safety. Water based products often out perform their solvent counterparts.
-Seth Kline
Hi Jeff,
Very nice and informative post on water based (borne?) lacquers. It answered both conscious questions and also ones I did not realize I had. One curiosity question ( you have to accept my total ignorance of coatings formulations and terminology), what is meant when you mention ‘propylene solvents’ in conjunction with some your water based lacquers?
Are you talking about propylene glycols, propylene carbonate (which is only moderately water soluble) or something entirely different? Just would be nice to know.
Thank you for educating all of us in addition to providing us with nifty materials to work with.
Regards,
Sandip
Sandip,
Thank you for your interest.
My reference to propylene solvents centers around P-Series glycols, of which there are over a dozen with various properties to choose from.
-JeffW-
Very interesting article on lacquers, especially comments on and from music instrument builders. I build Appalachian dulcimers, and my bent has always been to stay as close to the essence of early techniques as possible, while keeping an eye out for 20th century improvements that enabled better processes and results.
I was drawn to this article and its comments out of a concern that lacquers tend to check – only to find that is a desired quality for legacy instrument builders.
For myself, I jumped at the opportunity to use EM2000WVX at its earliest hybrivar introduction, finding that I could take advantage of its ability to serve as a wiping varnish, and compensating for an early difficulty with ‘wetting’ the wood by sealing with appropriately colored shellacs.
Though you may wish to not include this comment in the discussion, I couldn’t miss the opportunity to praise the capacity of your non-conversion varnish for its support of very low-tech hand application, excellent flow properties with a simple lintless pad, avoiding all the equipment, and accompanying complications of spray booths and exhaust, even brush cleaning, I can get 8 coats onto a musical instrument, each quite thin and burned-in to the previous, as fast as two hours, pausing only to wash my gloves to avoid dry-film creation. And If I don’t rub it out within 24 hours it is liable to be too hard to cut with #0000 steel wool.
Kudos!
Dwain,
Thanks for adding a comment and offering insights on how to use EM2000wvx as a wiping varnish on your dulcimers. You are part of a vocal group of customers who like to use EM2000wvx on their musical instruments and I think this is a great way to let others know there are options outside of our water-based lacquer type of finishes as well as alternate application methods outside of spray.
Thanks so much for adding to the conversation.
-SK
I think what throws people about water-borne lacquer is that isn’t truly an evaporative finish. One of the biggest pluses of old nitro-lacquers are that they can be thinned to any consistency and refinishing is easy since old lacquer can be dissolved with thinner. Of course, water borne is far safer and far less toxic. I’ve used the Em6000 and it is indeed great stuff. “Lacquer” really is the closest term to what it is but in many ways it is its own thing.
Sherri328.shs@gmail.com
Hi Jeff,
I am just a hobbyist with refinishing furniture. I am currently working on old antique outside wood benches with iron frame. I need to know the best, most protective, weatherproof and glossy product to use please 🙏.
Hi Sherri,
Thanks for your comment. I recommend you apply our EM9300 Polycarbonate Urethane as your topcoat over these wooden benches. We recommend a minimum of 4 coats for the best protection on exterior projects.
-Seth Kline