In Part 1 of this post, I opened a discussion on the growing popularity of waterborne 2K polyurethanes, also commonly called “2K WB’s,” “2K urethanes,” “2K-PU,” “two-part” or “2-pack” urethanes.
These are waterborne coating formulations that use a secondary additive in their design, making the coating a 2-component system.
With the use of 2K polyurethanes trending on social media channels, often with NOTHING being said about their potential hazards…
I decided to drill deeper into the topic, starting with the history of 2K waterborne coatings, how they are made, and why they are still available when self-crosslinking 1K and externally crosslinked waterborne technology is gaining popularity in the wood finishing markets.
What I found was some very interesting — and sometimes troubling — approaches to the 2K trend, both in what the formulators are branding as “two-component” in functionality, and the type of catalyst chemicals being marketed and sold to the unsuspecting tradesperson and DIY customer.
But, to better understand the current situation, let’s first take a brief step back and learn a bit more about the history of 2K coatings specific to the wood finishing trades.
First, let’s look at the terminology of “2K” in the realm of water-based coatings being marketed in 2021 to woodworkers and cabinet finishers.
Similar to the use of the term 2K in solvent-based coatings, as it is being used today in water-based formulas, a 2K system is simply a two-component formulation composed of a Part-A and a Part-B.
This coating system requires the blending of the two components together, in premeasured volumes, into a single, functional reaction that allows the resin to through-cure and not remain soft or tacky.
Common 2K systems from the 20th Century that are still in use today are solvent-based acid-catalyzed varnishes, and isocyanate catalyzed solvent-based urethanes.
Again, these older examples of 2-Component coating technologies require the use of an external additive (the “Part B”) to complete the chemical reaction. If the external additive is not blended into the resin in the correct proportions the reaction will not be complete, and the resin will not attain its intended physical properties.
What I see trending in the waterborne coatings market is the modification of the term 2K for use with water based polyurethane and acrylic lacquer finishes that will dry and cure to a film without the use of an actual catalyst — but are fortified with a blocked isocyanate in rather low percentages, much in the way a crosslinker is used.
The “Part-A” side of these 2K products are fully capable of drying and curing completely on their own accord without the addition of their respective “Part-B” affiliate. Whereas the traditional solvent 2K systems mentioned above absolutely require the addition of their allied catalyst to perform the curing mechanism.
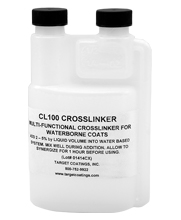
Like the trendy 2K WB’s, modern waterborne urethane and acrylic resin systems being marketed today will form a film and cure when exposed to oxygen alone. The addition of a less toxic chemical compound, correctly called a crosslinker, will enhance and fortify the final physical characteristics of the curing WB resin — also at much lower percentages by volume. An example of a crosslinking agent common in the early development of WB technology is aziridine – which is now out of favor due to its dangerous effects on regular users. Other, and far less hazardous crosslinkers are carbodiimides, siloxanes and specialty ester diols such CL100 Crosslinker.
Yes, catalysts and crosslinkers function differently on a chemical level, but this functionality (and incorrectly using the terms interchangeably) is NOT what has me, and others, concerned.
Rather, it’s that the additives being sold as part of a “modern” water based 2K polyurethane system containing highly toxic modified isocyanate blends, and in some rarer instances polyfunctional aziridine, are being promoted as user and environmentally safe.
The use of aziridines and perhaps more importantly, isocyanate compounds at low but still hazardous percentages in waterborne paint and clear coat systems being marketed today leads to a further blurring of definitions between catalyst and crosslinker, as well as user and environment safety…
And one must question why these very toxic additives are being sold to a customer base that should not be exposed to these chemicals and/or doesn’t realize the higher levels of safety protocols required to use them.
We’ll go into detail about these additives in Part 3 of this post, so stay tuned.
For now, please keep your questions and comments coming about 2K polyurethanes. Please share your thoughts or read what others are saying in the comments section below.
Hello,
One of my family members is now working full time in his wood shop. He recently visited a demo with the popular “M” brand. I am an avid user of Target coatings and I had him ask the rep about the safety of their product. The rep stated that the isocyanates are contained in the paint so as long as you are not breathing the paint you are ok. The rep laughed about the question as if it was ridiculous to ask. I find that hard to believe and border line irresponsible. Hopefully I can convince him not the use the product but he is really impressed with the finish.
Mike – Thank you for sharing your anecdote with us. There are specific protocols and procedures that need to be followed when handling MDI, HDI and Blocked Isocyanates. Each have their own reaction and functional qualities, but all require specific industrial hygiene requirements to ensure that the user is well protected. We’ll focus on this aspect in a future post. In the meantime, I recommend that your family member reviews the SDS (Safety Data Sheet) of the catalyst in question to determine the exact safety procedures required to protect him/her/they-self to ensure correct safety on handling and use.
-JW-
Jeff, 1st thanks for the important information. I am a fan and user of Target Coatings due to product performance and you being accessible. Not to ignore the health risks, but what is the functional product performance of Target crosslinked products vs these “2K” products? It seems it would primarily be abrasion resistance, separation/delamination, chemical resistance, UV resistance type performance characteristics.
Most of the “2K” products in question are positioned as conversion varnishes, so the appropriate Target product to compare to is 8000cv. Furthermore, if you’re willing to deal with mixing in a catalyst then you should probably compare to 8000cv with EM100 additive.
I won’t name the competing isocyanate-catalyzed “2K” that I use here, but I would say that from a mechanical durability perspective there really isn’t much in it. Both finishes are fairly bombproof, at least by my standards. I haven’t systematically compared UV resistance, but I wouldn’t expect any huge difference there. Where I think I see a difference is in how they handle some solvents (lacquer thinner, alcohol) and ammonia. Both finishes will recover from exposure (or at least the sorts of exposures I’ve tried), but the “2K” seems to soften significantly less and recover to full strength more quickly. My $0.02 of observations, FWIW, YMMV.
One other difference is that the 2K cures faster, which may or may not matter to you.
As I said in another comment, I think that it’s entirely possible to use those 2K finishes safely, but you do have to adhere to more rigorous industrial hygiene than with the anything in the Target line. It’s reassuring to look at an SDS and see “None Of The Ingredients In This Product Meet The Definition Of “Hazardous Chemical” Given In The OSHA Hazard Communication Regulation 29CFR 1910.120 (C)”. The 2K catalyst SDS’s read a bit differently.
On a related note, both EM100 and the “2K” catalysts have to be mixed with some care to avoid a “grainy” finish. After a few false starts I settled on using a magnetic mixer (with a big 90 mm rare-earth stir bar) and a syringe with a long 10-gauge tip to gradually inject the additive into the vortex.
I think there is a lot of misinformation and exaggeration going around on this.
On the previous post several commenters compared the chemicals in question to the ones used at Bhopal. No, that was methyl isocyanate, which is far more toxic than any of the isocyanates used in “water based 2K” catalysts. Methyl isocyanate has an NFPA class 4 health rating (“extreme danger”, will kill you in a heartbeat), whereas the ones in 2K conversion varnishes are typically in class 2 (can “incapacitate or injure” you with “intense or continued exposure”). There is a world of difference between those and to imply otherwise is to spread blatant disinformation.
The reason that supplied air is recommended with isocyanates isn’t because standard activated charcoal organic cartridges don’t work effectively to block it (they do), but because the substance is deemed not to provide sufficient indication when the filter becomes saturated and stops working, i.e. a saturated filter may let in a harmful amount of the substance before you smell it. While I would never suggest that anybody else take a particular course of action, I use a belt-mounted PPA system, and “schedule” my filters such that I only use them with isocyanates when they are fresh. I’m also extremely conservative in terms of how long I use them.
I use and love several Target finishes (especially EM8100cv). I also use an isocyanate-catalyzed water-based “CV” in some specific situations where I need the best possible chemical resistance. When I do I spray in a very well-ventilated room, wearing PPE including the aforementioned positive-pressure system. It’s not great stuff to be around (which is why I default to the Target finishes) but it’s also not the end of the world. As Jeff says you need to understand and respect what you’re dealing with. No more, and no less.
What intelligent, informative, mature and civil discussion, like a breath of fresh air.
As a floor finisher I mostly use single pack oxygen cross linking water based polyurethane and some two pack isocyanate cured polyurethane.
The hardener is a mild skin sensitiser but quite a potent inhilation hazard. I am not sure how much of the isocyanate would remain unreacted once mixed and let to dwell for a few minutes before atomisation but the above post by Patrick seems eminently sensible for those who spray it.
As a roller and brush applicator I guess my exposure levels are quite low unless there remains a large excess of unreacted isocyanate that off gases during curing.
Toby – Thank you for sharing your thoughts on this topic with us. We look forward to your participation.
-JW-