As we transition into the dog days of summer, now is a good time to talk about the potential challenges of wood finishing in warm weather.
As we have discussed in a previous article about wood finishing in cold temperatures, wood coatings can be sensitive to environmental conditions and therefore different techniques for application may be necessary.
For example, oil-based coatings and nitrocellulose lacquers are more sensitive to the high humidity that often comes with warmer temperatures in many parts of the country.
This high humidity can lead to unsightly blushing or trapped moisture in these coatings.
Fortunately, moisture blushing is rarely an issue with good quality, high-performance water based coatings and sometimes high humidity can balance out the rising air temperature.
Unfortunately, warmer temperatures or dry conditions can lead to rapid flashing off of the coating and this usually results in texture or overspray lines that most finishers want to avoid or eliminate.
Let’s take a deep dive into what you can do about this, including why you might want to consider using Emtech SA5 Retarder not only as additive for your favorite clear topcoat but as a useful addition to any Target Coatings product.
Why Wood Finishing in Warm Weather is Challenging
As temperatures rise and/or humidity drops, your coating is going to begin to dry much faster than during the cooler months. To some extent these conditions are welcome and will reduce drying and curing times which means a much faster turnaround time in the shop.
However, as conditions continue to warm up and dry out, you may begin to run into some problems and visible imperfections that you didn’t have when the temperatures and conditions were more favorable.
This is because the coating begins to flash off almost as fast as you’re applying it and you’ll see overspray marks or lines; skips become more visible; it’s harder to avoid orange peel on the surface; and you see a lot more texture when using hand application techniques like brushing and rolling.
All these imperfections are a result of the coating drying or “flashing off” too rapidly and not having enough time to level out.
Warmer temperatures and/or low humidity means faster evaporation of the water and co-solvents in the coating which reduces the time necessary for proper flow out.
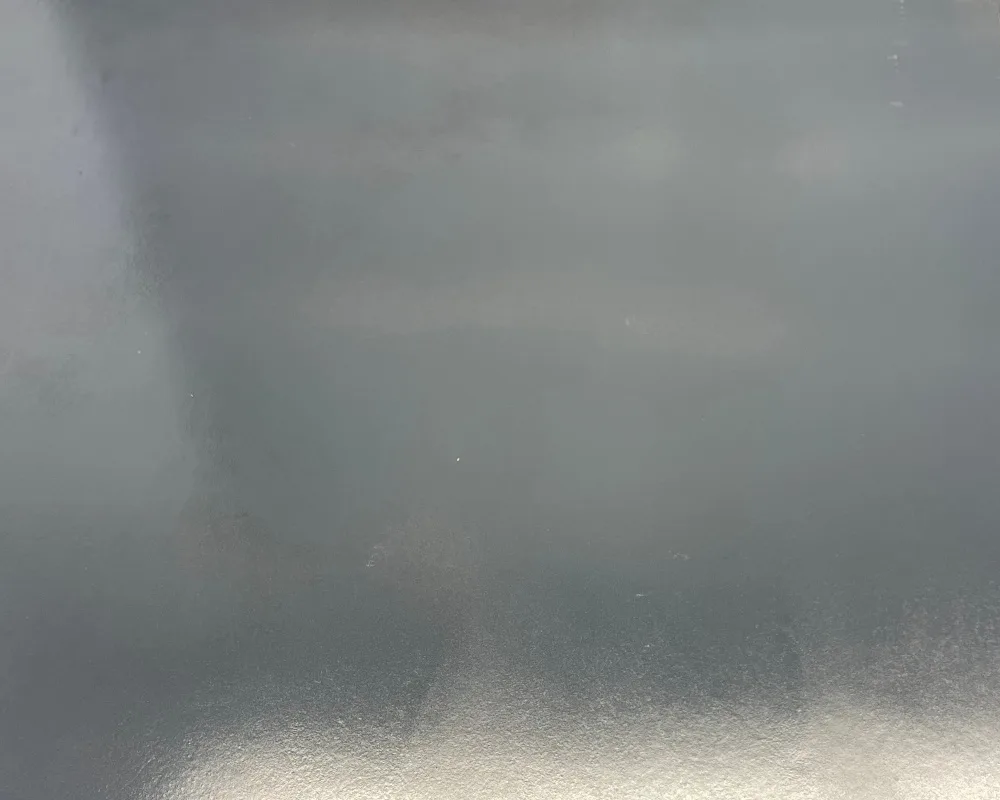
How to Avoid Warm Weather Problems
In certain conditions when you might only need a small adjustment, adding a little water might be all that’s necessary. Adding some water can slow down the evaporation of the coating enough that you’ll see appreciable results.
Unfortunately, while water will dilute the coating and slow down evaporation it doesn’t help as much with the flow out of the coating as it’s drying. This is where Emtech SA5 Retarder can really come in handy.
SA5 Retarder binds with components in Target Coatings products which not only prevents the coating from flashing off too quickly but also increases the flow out and leveling of the coating as it’s drying.
Even when conditions are perfect, sometimes the addition of 5-20% by liquid volume can be very helpful on large and difficult to spray projects. Giving you extra time to complete your spraying and allowing the coating time to level out and smooth over your less than perfect spray technique.
Addition of SA5 Retarder at 5% by liquid volume in clear topcoats like EM8000 Conversion Varnish can also help reduce orange peel or visible texture of the coating when spraying thicker wet films.
While EM2000 Waterborne Alkyd Varnish is extremely brush friendly and rarely needs the addition of retarder for brush application, almost all of our other coatings benefit from at least a small of SA5 Retarder when using hand application techniques even when the weather is perfect.
Brushing can be slow work on a large surface and the retarder can help with maintaining that “wet edge” as you work across your project.
Rolling often introduces a lot of air bubbles on the surface during application and the retarder not only reduces the viscosity of the coating helping to break up these bubbles, but gives the additional time necessary for the coating to flow out for a smoother final surface.
Take a look at the two samples below. In the first image, we can see how the retarder added into the EM9300 Polycarbonate Urethane on the right side produced a more level and smooth finish vs. the left side.
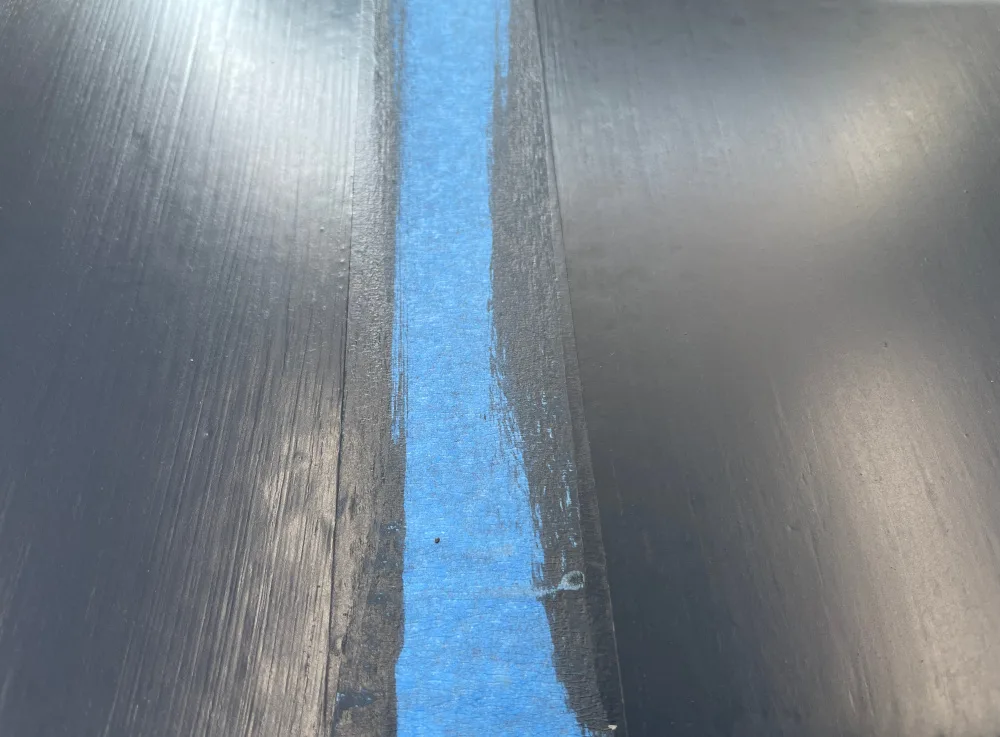
In the next image we can see how the retarder added into EM6500 Pigmented Lacquer brush applied over a light background leveled out and covered the substrate better on the right side, while on the left it looks streaky.
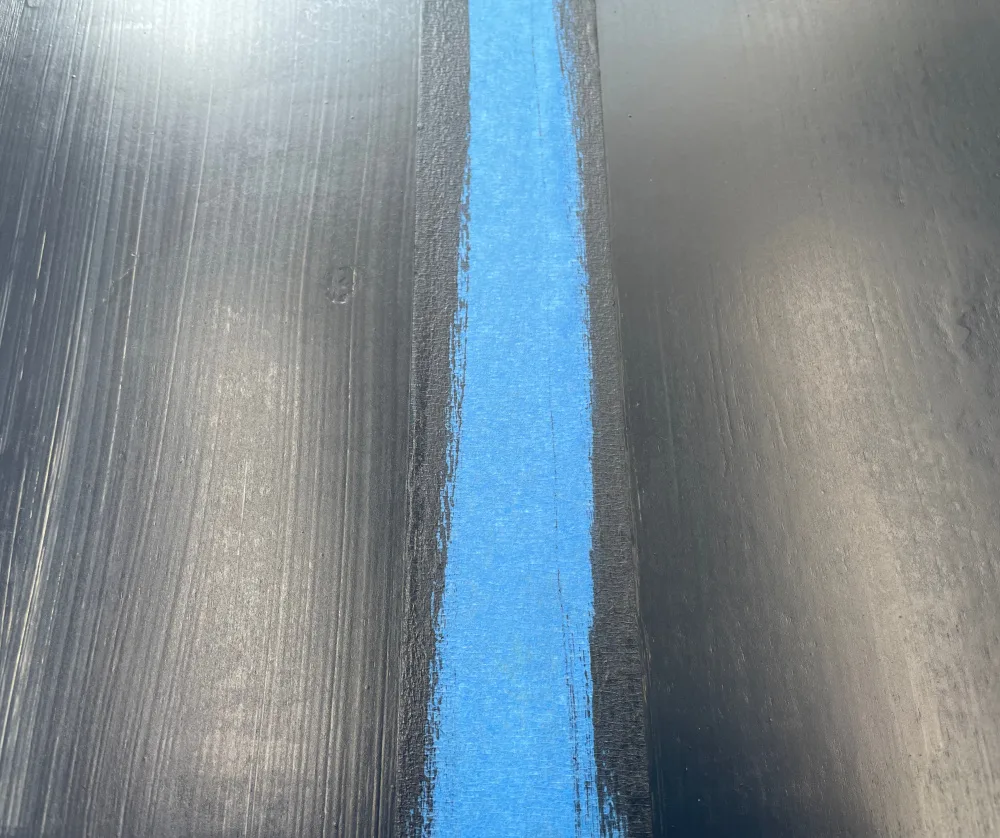
I would like to point out that while SA5 Retarder is a useful additive and can benefit the finisher in a multitude of ways, one needs to be careful in certain circumstances, especially when the coating is applied thickly and/or on a vertical surface.
As you can see in the image below, while the retarder did an excellent job of leveling out the coating on both sides of the sample, the coating to the left was applied too thickly and, given the extended dry time, produced a sag and run in the finish.

Often these imperfections can be sanded flush when fully dry and a few light passes can blend everything together, but definitely something to be avoided whenever possible.
Also, please remember that the retarder does slow down the overall dry time and not just the initial set time of the coating. This means you might need to wait a little longer between coats to be sure the surface is adequately dry before application of additional coats.
As a final note, I would like to point out that SA5 Retarder only nominally increases the VOC of the coating. This is an important aspect of using this additive and knowing that it does not dramatically alter Target Coatings’ already safe to use and low VOC formulations.
I think that sums up our tips for wood finishing in warm weather and the benefits of using SA5 Retarder.
Do you adjust your finishing in warmer weather, and if so, what do you do? Have any questions about what you just read? Please share your thoughts or read what others are saying below in the comments section.
Seth Kline has been a woodworker, wood finisher and business owner for the past 25 years. After helping grow his family’s home remodeling firm — Roy B Kline & Son — both as a craftsman and business operator, in 2013 Seth became the co-owner, lead woodworker, and shop manager of Stor Handmade Furniture, a highly successful solid wood furniture shop specializing in bespoke, hand-made and hand-finished pieces. In 2023, Seth launched SBCraftsman, which offers spray finishing and small business consulting to private clients. Originally from Pennsylvania, Seth now resides in Aberdeen, N.J., and is a proud member of the Central Jersey Woodworkers Association.
Seth, another super article! You mentioned that SA5 Retarder slows down the drying time, but does it also extend the full cure time beyond the usual 120 hours for most finishes?
Please keep your excellent articles coming!!
Marty,
Thanks for your insightful question in this comment. SA5 Retarder, in most circumstances, does not significantly alter the overall cure time of the finish. The primary purpose is to slow down the initial drying phase and set time of the coating to allow for more effective leveling before the coating sets up. Most of the components that make up the retarder evaporate off during this initial drying time and therefore will not have an effect on the recommended 120 hour cure time. In some unusual circumstances where a finisher might use a high percentage of retarder (15%-20%) during cooler temperatures or in a very high humidity environment, they might want to consider adding extra time to allow for a final cure of the finish. However, this is usually true for most water based finishes even without the use of retarder.
-Seth Kline
Love the articals please keep them coming! Can the retarder and cross linker be used together or is there any kind of interference? In central Texas the retarder has helped significantly, but I have a few projects coming up that would benefit from the cross linker as well. Thanks.
Hi Taylor,
Thanks for your comment. Yes, both the CL100 Crosslinker and SA5 Retarder can be used at the same time. I recommend you first mix the CL100 at the recommended amount by volume into the coating, and after mixing for 2 minutes, allow the coating to rest a few minutes. Add your desired amount of retarder and continue to mix for additional 2 minutes. After mixing the retarder, allow the coating to rest an additional 60 minutes before application.
-Seth Kline