My last article explored the value and purpose for using Target Coatings SA5 Brush and Spray Retarder, especially in warm and/or dry weather environments. For this post, I’ll explain how and when you might want to use the other additive Target Coatings offers, CL100 water-based crosslinker.
Part 1: What is a Crosslinker (vs. a Catalyst) and When Should You Use One?
Generally speaking, crosslinkers and catalysts create better adhesion, better scratch resistance, better water/chemical resistance and better gloss retention in a final finish.
The big difference is HOW they do it.
Whereas traditional catalysts and crosslinkers employ dangerous, highly reactive chemicals such as isocyanate or aziridine, which are incorporated to facilitate the curing mechanisms of the resin they are being added into, our CL100 water-based crosslinker is a safer, water-soluble additive that reacts with oxygen in the air to tighten up the resin structure of the Emtech coating as the wet film is drying on the surface of your substrate.
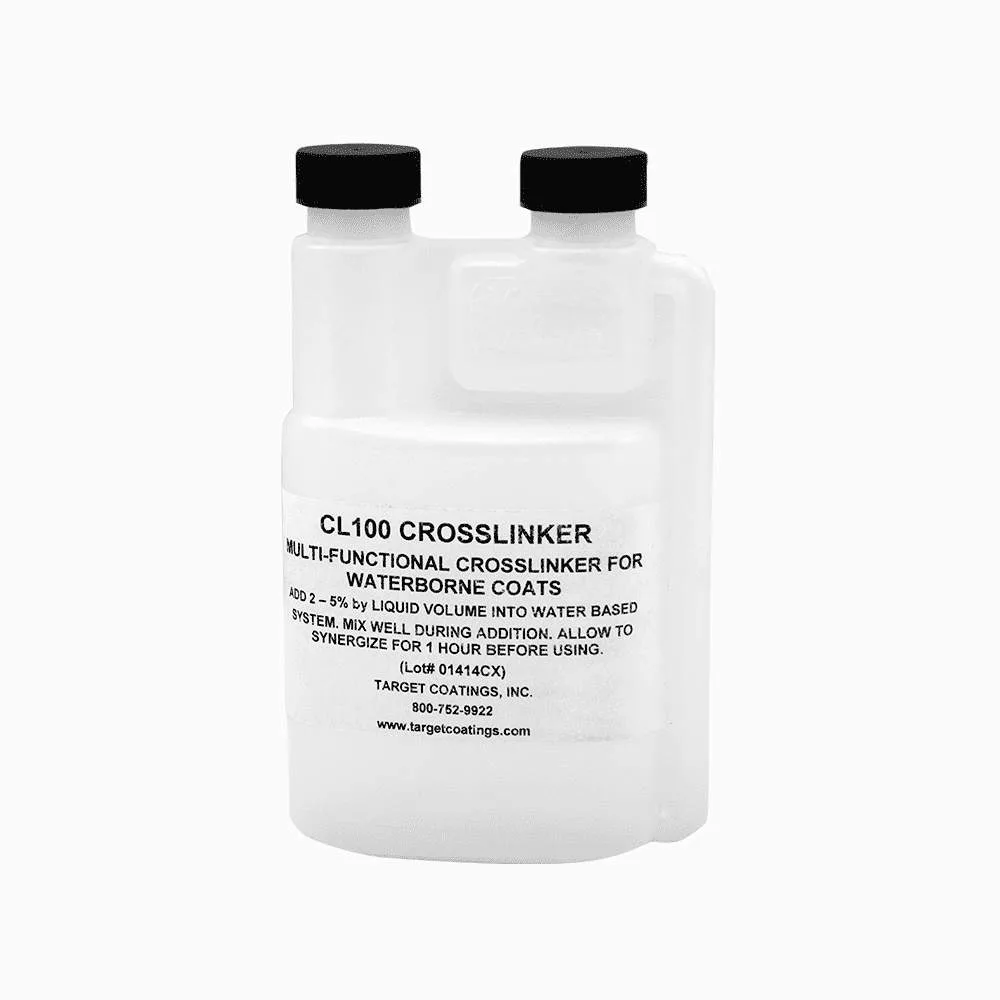
On a molecular level, the crosslinker draws the resin molecules closer together, creating a reaction that results in a harder, tighter bond which creates a harder, tougher shell – thus enhancing the performance of the final film of the coating.
The addition of CL100 into any Emtech® coating (excluding NR4000 Stains) has multiple benefits…
- Promotes better adhesion to difficult-to-coat substrates
- Creates a harder final film that is more scratch and mar resistant
- Creates a final film that is more water and chemical resistant, allowing for longer exposure time to high pH cleaners, alcohols, and corrosive chemicals.
- Creates overall better gloss retention in the final film as the coating ages

Again, most importantly, CL100 Crosslinker does not contain isocyanate or aziridine, two toxic chemicals often used in catalysts and crosslinkers for coatings by other manufacturers to harden final film builds.
These chemicals are harmful to finishers and others exposed during application and drying of the coating.
CL100 also does not substantially increase the low VOC content of any Target Coatings water based lacquer or clear topcoat. This is especially important for on-site applications and knowing that an enhanced coating doesn’t have to be at the expense of your health and safety.
A Note about 1K vs. 2K
Let me just stress here, strictly speaking, adding CL100 Crosslinker into an Emtech® coating does NOT create a 2K coating.
Crosslinking is not a true catalyzing function and I do not want to confuse anyone and compare the use of CL100 as being the same as a true 2K product.
Resins in a 2K product require catalyzation and will not completely dry or fully cure without the use of the required catalyst.
By contrast, the resin in an Emtech® coating will still dry and cure on its own, but the crosslinking function makes the resin being crosslinked exponentially more durable in all of its physical characteristics by creating a post-catalyzed type of finish.
When to Use a Water-Based Crosslinker
Now that we explored how CL100 works and what it does for the coating, let’s dive into WHEN you should consider using this additive.
As I’ve mentioned previously, the Target Coatings Emtech® line of coatings are already outstanding on their own, and in many cases adding this enhancement could be more of a hassle and expense than it’s worth.
In some cases, you may want to consider using CL100 for part of your project vs. the whole thing.
For example, kitchen and bathroom cabinets. Both often get a lot of abuse and would benefit from an enhanced coating, but it’s probably best not to “waste” CL100 on the cabinet carcass interiors.
Except for maybe the sink base, none of the abusive action happens inside the cabinet. I think a better use of CL100 is on cabinet doors, drawer fronts, and maybe exposed face frames. This is where all the constant touching, spills, and cleaning can wear down the finish over time and cause problems.
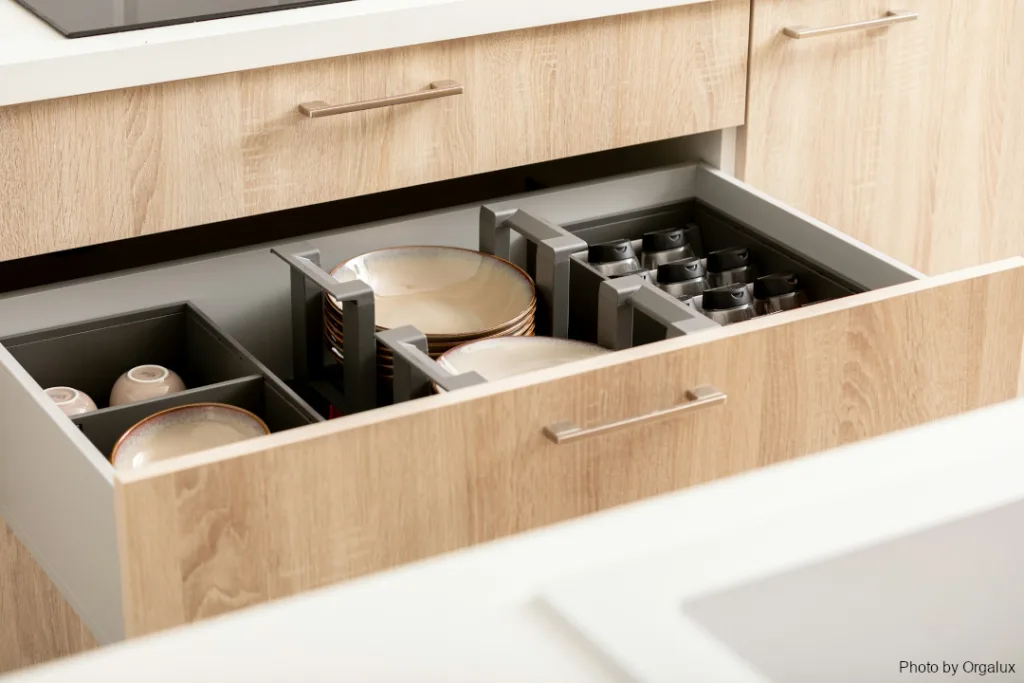
Other uses could be for light commercial settings like bar tops and work cabinets. These projects often see very frequent use from patrons and cleaning from the staff that can prematurely break down coatings.
What about hardening up the final film for better scratch resistance?
While our EM8000 Conversion Varnish tends to be pretty hard all on its own, EM2000 Waterborne Alkyd Varnish and EM9300 Polycarbonate Urethane tend to have a softer, more flexible film build.
The latter two work great for exterior environments where you need that flexibility to take up the movement from temperature and humidity changes, but you may not want that for interior projects. Additions of CL100 into these coatings at 5% by liquid volume, for interior projects only, can greatly increase the final film hardness and give you more scratch and mar resistance.
Luthiers and instrument finishers may want to occasionally consider the use of CL100 as well. Hand and body chemistry of each person is unique and sometimes the combination of a person’s natural oils, sweat and/or hand lotion can cause the finish to break down prematurely.
Adding CL100 to our water based lacquers — EM6000 Production Lacquer or EM7000 High Build Lacquer — at 3% by liquid volume can boost the chemical resistance of these coatings and help instruments stand up to daily use (or abuse!) by their musicians.
As you can see, there are multiple uses for CL100 Crosslinker, but focusing on areas or projects that truly need it can be cost effective and save time.
Part 2: Tips and FAQs When Using Crosslinkers
One of the best tips I can give you when using a crosslinker is to add it to more than one coat for the best results.
I recommend using it in at least three coats. If you plan to apply five coats of finish to your project, then you can skip the first two coats and reserve the crosslinker for the final three topcoats.
When it comes to mixing a crosslinker into your coating, I should point out that Target Coatings most recent formulation of CL100 Crosslinker incorporates into the coating better than ever.
I’ll spare you the chemistry, but just know there is an improved synergy with the resin in the coating which means a better reaction as the coating dries, boosting performance of the final film build to its highest level.
Here are a few more tips on how to get the most out of this additive and boost the performance of your Emtech® water-based finishes:
First, there’s a great video where Jeff Weiss outlines how to add CL100 into your preferred coating.
You can check out the video below, but please note: this video was made with the EARLIER version of CL100 where it was really important to mix correctly and was often very intimidating to finishers to use this additive in their coatings.
Again, the most recent formulation of CL100 is MUCH easier to add compared to the one in the above video, and as long as one is gently stirring their coating during a slow addition of the additive, there are typically no problems.
What is the right amount of CL100 to add?
It depends on your coating of choice. Emtech® lacquer formulas EM6000, EM6500, EM6600 and EM7000 will not benefit from more than 3% by liquid volume.
Adding more to these coatings will not get you any extra enhancement so it’s better to conserve the crosslinker and add 3% or less. The rest of the Emtech® clear finishes will gain benefits with up to 5% by liquid volume.
Check out the Target Coatings Product Comparison page for a section on the maximum amount of crosslinker to be added for each coating. This sheet can even be printed in PDF form for easy future reference.
Another question and concern I hear a lot is…
“What about using SA5 Retarder in tandem with the CL100 Crosslinker?”
This is also not a problem. My general guidance is to add your CL100 first, measuring out by liquid volume of the coating.
After proper stirring of the mixture, allow it to settle for 2-5 minutes before adding your retarder by liquid volume of the original coating measurement.
Allow the combined formula to rest a minimum of 30-60 minutes before you begin using it to allow for all the components to properly synergize.
What is the “pot life” of a CL100 crosslinked coating ?
When we examine the CL100 Crosslinker TDS, the enhanced synergy and functionality of the coating is active for about 100 hours. After this time, you should add a small amount of CL100 into the mixture to refresh and activate the crosslinker again. This feature can help extend your 100-hour functional pot life and help reduce waste of product.
In previous formulations of CL100, I was able to get a very long shelf life out of a coating enhanced with CL100, sometimes several weeks or months.
Recently, I’ve noticed the coating will begin to gel slightly or form small hardened nibs even when sealed in an airtight container. This reaction is accelerated by unusually warm temperatures and oxygen, but time is also a factor.
Tips to Reduce Waste
There doesn’t seem to be an exact time frame for when the coating no longer becomes usable, but I suggest the following guidelines to reduce waste and prevent potential issues:
• Only mix enough coating that you will realistically use within 1-2 weeks.
• Store any unused mixture in an airtight container and in a cool dark place.
• Do not allow the mixture to sit in spray equipment or guns overnight. Clean your equipment at least once per day.
• Always strain your mixture with a 200 micron fine mesh nylon strainer to remove any nibs that may have hardened in the coating over time.
• If the coating thickens, add 5-10% water by liquid volume to reduce slightly and make it more spray friendly.
• If the mixture gets too thick or chunky, it’s time to properly dispose and make a new batch.
Funny story, I recently was preparing for a demonstration on the addition of CL100 into a coating. I prepared a mixture the day before the demonstration and stored it in my car late afternoon and overnight. The warm temperatures that built up in my car warmed the coating and accelerated the reaction.
The next day when I opened my bucket for the demonstration, my coating had thickened substantially. Fortunately, some water reduced the coating and kept me on track with fantastic results. However, fair warning, do not store your unused mixture in a hot car or on a sundrenched window sill!
This leads me into my closing tip and suggestion.
Temperature Matters for Best Results
As I’ve mentioned, CL100 responds very favorably to heat.
This can be a problem in cooler months where you are struggling to keep your drying space warm. It’s really important that you allow projects with a CL100 enhanced coating on them to dry in a 70°+ F environment to get the best results from this additive.
Cooler temperatures can actually slow down the overall cure time. If you’re unsure how to create a warm space for drying, check out this article I wrote for Target Coatings on How to Finish during Cooler Weather.
If you have any crosslinker comments or tips of your own, please share them in the comments section below. If you have further questions, please feel free to contact me through the Target Coatings contact form.
Seth Kline has been a woodworker, wood finisher and business owner for the past 25 years. After helping grow his family’s home remodeling firm — Roy B Kline & Son — both as a craftsman and business operator, in 2013 Seth became the co-owner, lead woodworker, and shop manager of Stor Handmade Furniture, a highly successful solid wood furniture shop specializing in bespoke, hand-made and hand-finished pieces. In 2023, Seth launched SBCraftsman, which offers spray finishing and small business consulting to private clients. Originally from Pennsylvania, Seth now resides in Aberdeen, N.J., and is a proud member of the Central Jersey Woodworkers Association.
Thanks for a very informative article. What are the long term effects for refinishing and/or touch up. If you wanted to refinish an area, or a whole item 5 years or even 10 years later will you get the same adhesion going over em 6000 or 7000 with the cross link vs without the cross link?
Hi Bob,
Thanks for your comment. There’s no reason adhesion over a crosslinked coating should be an issue over the long term provided the surface is free of contamination. While the crosslinker helps tighten the bonds in the resin making the film harder and more durable, it does not alter the final state of the coating film build. It would not hurt for you to add the CL100 Crosslinker into any future coats you add over a crosslinked coating. The CL100 will boost adhesion and form a tighter bond with the existing crosslinked coating.
-Seth Kline