Many woodworkers consider woods with a high oil and rosin content to be among the most beautiful materials available, but finishing oily woods has historically been a challenge to accomplish properly and safely.
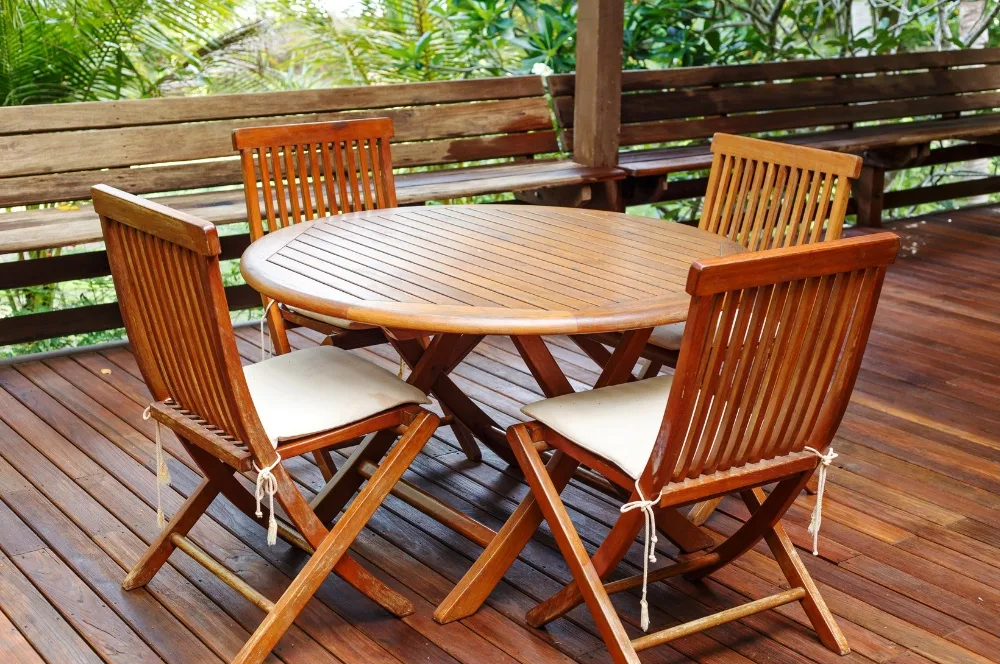
While the correct surface preparation of the selected wood species is important, the methods of preparation come from various schools of thought.
Traditionalists tend to resort to cleaning the wood multiple times with acetone or denatured alcohol before and after each milling and sanding procedure (to remove the inherent oil), sealing it with dewaxed shellac, and finishing it with nitrocellulose lacquer, penetrating oil-varnish, or 2K catalyzed finishes.
These processes bring several safety factors into focus – In addition to the array of chemicals used to clean and neutralize the oils – let alone the chemical composition of the solvent-based finishes, many being highly flammable, finishers are exposing themselves to the dangerous toxins found within the wood species itself.
I’m happy to report there is now a safer, highly effective, water-based way to finish oily woods and other challenging substrates. (Spoiler alert: see EMCAT+ Si427 Sealer Isolator.)
More on that in a bit.
To understand the full picture, here’s what you need to know about working with and finishing oily woods.
Common Oil-Rich Wood Species
The term “oily woods” refers to several exotic hardwood species that contain naturally high levels of oils and resins within their cellular structure. The most commonly used oily woods include:
• Teak: Perhaps the most famous oily wood, prized in boat building and outdoor furniture
• Ipe (Brazilian Walnut): An extremely dense South American hardwood
• African Rosewood: Various species known for their rich, vivid colors
• Cocobolo: A tropical hardwood with striking grain patterns
• Babinga: Known for being troublesome when finished with oils
• Brazilian Walnut: Not to be confused with American Black Walnut
• Curupay: A South American wood species used in the flooring industry
These species are typically tropical or subtropical in origin, which explains their high oil content – it’s a natural defense mechanism against decay and insects in their native humid environments.
Benefits of Working with Oil-Rich Woods
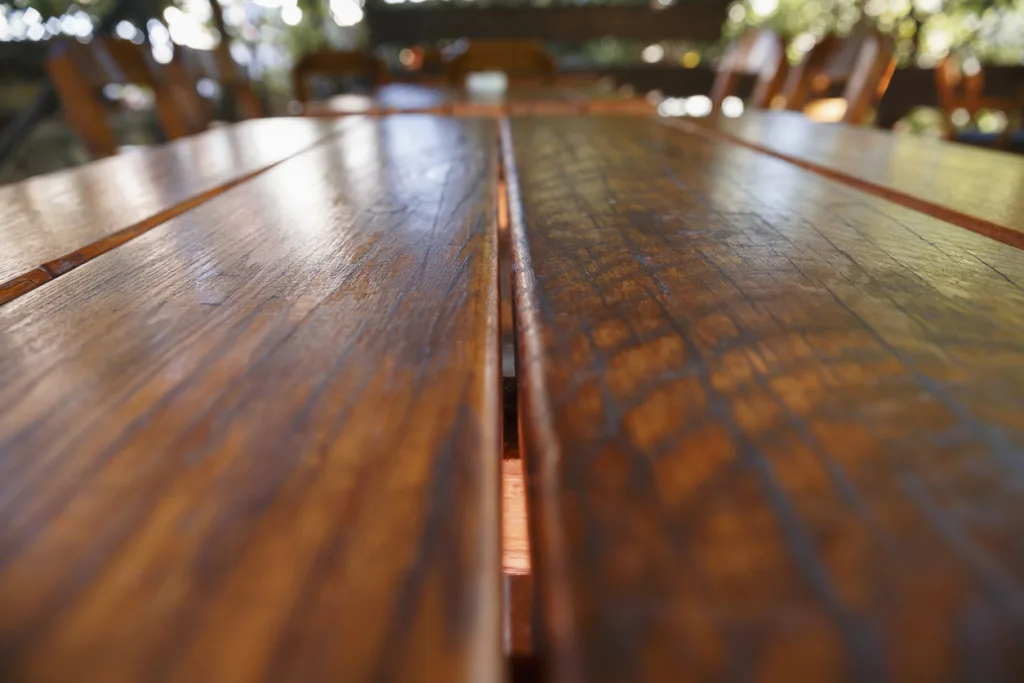
Despite the challenges of finishing oily woods, they offer several significant advantages that make them highly desirable for specific applications:
1. Natural Weather Resistance: Their high oil content provides excellent protection against moisture, rot, and decay, making them ideal for outdoor projects and marine applications.
2. Durability: Most oily woods are extremely dense and hard-wearing, often lasting decades with minimal maintenance.
3. Insect Resistance: The natural oils act as a deterrent to wood-boring insects and other pests.
4. Dimensional Stability: These woods tend to experience minimal movement with changes in humidity, reducing the risk of warping or cracking.
5. Beautiful Aesthetics: Oily woods typically feature rich colors and striking grain patterns that can be enhanced to create stunning finished pieces.
Historical Finishing Challenges
The characteristics that make oily woods desirable also create significant finishing challenges and explain why special preparation techniques have historically been necessary.
Whereas domestic hardwoods and softwoods readily accept finishes through absorption into the wood fibers, oily woods present unique challenges because:
• The natural oils prevent proper adhesion of many finishes
• Traditional oil-based finishes often remain tacky or fail to cure properly
• Conventional water-based finishes tend to blush on the surface
• The oils can continue to seep out of the wood over time, causing adhesion failure
• Temperature changes can cause the oils to become more active, leading to finish degradation
These challenges led to the development of specialized preparation techniques and finishing products specifically designed for oily woods.
Part 2: Preparation, Sanding and Sealing Oily Woods
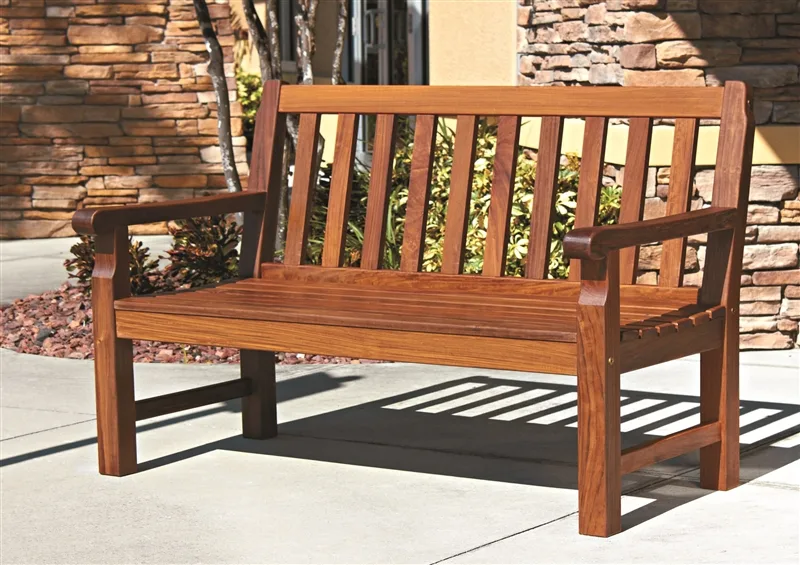
Preparing oily woods for finishing was historically labor intensive, but the extra effort was essential for achieving desirable results.
The traditional preparation process included…
1. Surface Cleaning: wiping the wood with acetone or naphtha to remove surface oils.
2. Sanding: progressively sanding and cleaning between grits.
3. Final Oil Removal: wiping again (and again, and again, etc.) with acetone, lacquer thinner, or denatured alcohol.
4. Sealing: applying a coat (or coats) of dewaxed shellac.
If that sounds like a lot of work…it was.
Thankfully, there is a newer, safer and faster way to prepare and seal oily woods.
In late 2024, we introduced EMCAT+ Si427 Sealer / Isolator, a water-based, self-leveling sealer and barrier coat designed specifically for use on difficult-to-cover substrates like oily woods and previously-applied coatings.
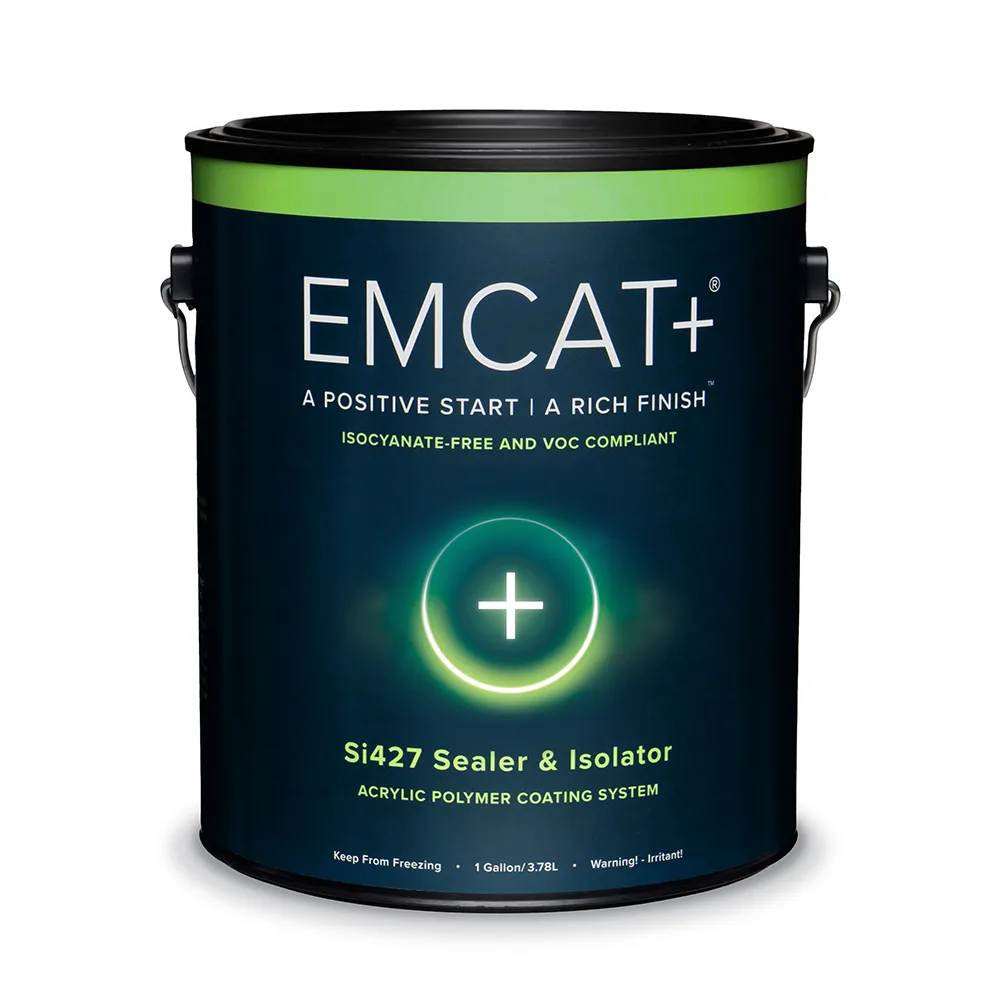
See, EMCAT+® Si427 features a unique ionic charge that allows it to bond to a wide variety of properly prepared substrates including all types of wood surfaces (oily, exotic hardwoods, veneers, engineered wood products, etc.), and a wide variety of natural and synthetic surfaces such as stainless steel, stone, plastics, and fiberglass.
This makes the process of sealing oily woods MUCH faster, easier and safer. All you need to do is…
1. Clean the wood surface with denatured alcohol or clean water
2. Sand to 180-400 grit based on your desired finish.
3. Apply Si427 via spray (rolling or brushing is recommended only on small areas)
By the way, EMCAT+ Si427 can also be used as a Sealer/Isolator over select fire retardant coatings without the concern of haze or chemical blush in the topcoat (I’ll cover this in detail in a future post).
The final step in finishing oily woods is, of course, top coating, which we’ll discuss in Part 3 below.
Part 3: Finishing / Topcoating Oily Woods
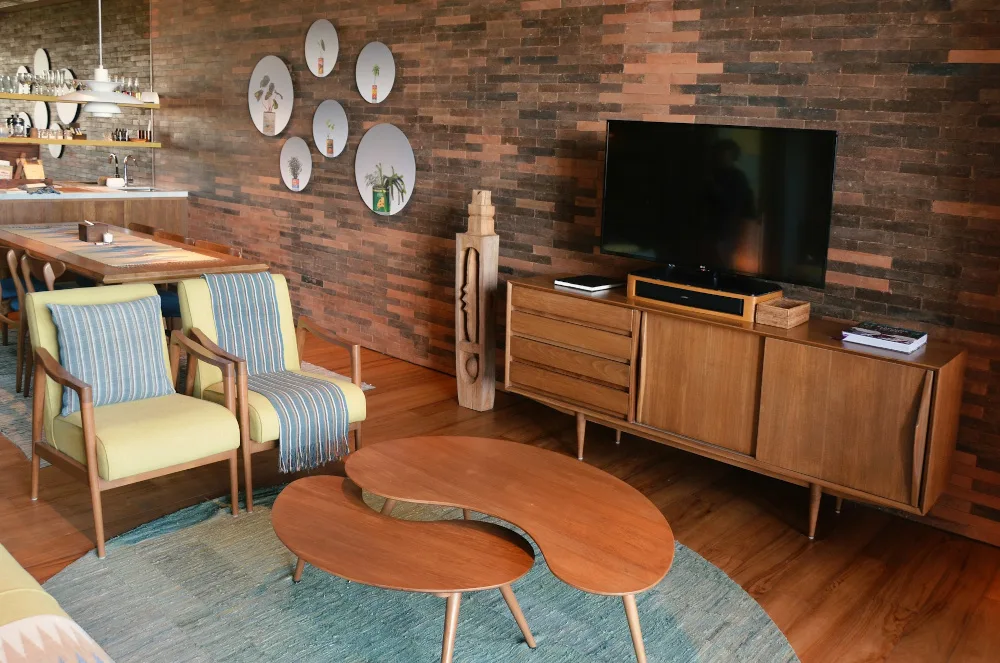
This is the moment of truth.
After carefully selecting your exotic wood and spending hours working it into something functional, it’s now time to finish it into something beautiful…and to protect that beauty.
Before we get into the performance and safety of finishes that ARE compatible with oily woods, let’s first review which finishes are NOT compatible and why:
AVOID THESE WHEN FINISHING OILY WOODS:
Traditional Oil-Based Urethane & Varnish presents significant challenges when applied to oily woods. Due to the oil content in-question, and even with meticulous preparation, poor adhesion remains a common issue with solvent-based oil varnishes and oil-modified polyurethane coatings as the natural oils in the wood continue to resist bonding with the finish, potentially leading to peeling or flaking over time.
Danish Oil and Similar Oil Finishes prove largely redundant when working with naturally oily wood species. Applying additional oils to woods already saturated with their own natural oils creates a problematic situation where the finish may never fully cure to provide adequate protection to the wood fibers. Penetrating oils may create a deep, wet-looking on the surface, but they are prone to attracting dirt and the substrate remains vulnerable to damage.
Standard Water-Based Finishes typically struggle with oily woods unless specifically formulated to address these challenging surfaces. On oily woods, these finishes may not level and flow-out to their best ability which may result improper penetration and adhesion. The result is often a frustrating experience requiring excessive coats to achieve even marginally acceptable results, wasting both time and material in the process.
OK, now let’s talk about the pros and cons of….
FINISHES THAT ARE COMPATIBLE WITH OILY WOODS:
Shellac has historically been the finish most people use on oily woods — its natural resin forms a physical bond, creates a barrier, and provides an amber glow. The downside is…shellac offers relatively poor alcohol resistance, making it less suitable for kitchen tables, bars, or bathroom surfaces. Plus, its shelf life once mixed is quite limited, typically just a few months, requiring careful planning and potentially more frequent purchases.
Two-Component (or 2K) Catalyzed Finishes chemically react to form extremely durable bonds even on challenging oily substrates, and their high chemical and moisture resistance make them good for high-traffic commercial applications. The downside is...the safety concerns are significant as we’ve discussed here. These finishes typically contain isocyanates that pose serious respiratory hazards during application, requiring proper ventilation systems and appropriate respirator protection. The mixing process introduces room for error, too, and once catalyzed, you face a limited pot life — use it or lose it. Their high VOC content also means they’re increasingly restricted in many regions due to environmental regulations.
Wiping Varnish is usually a modified oil-based varnish thinned for wiping applications. Its thinner viscosity allows for better penetration and adhesion on oily woods. The downside is…you typically need to apply multiple thin coats to build any kind of durability and this can add significantly longer cure times (potentially 24-48 hours between coats). And of course, these oil-based varnishes emit higher VOCs during application and the extended drying times.
Specialized Water-Based Finishes for Oily Woods are, in my opinion, the best choice for finishing oily woods. If formulated correctly, they provide the best of all worlds: a much safer alternative to solvent-based 2K finishes, fast cure times, AND extremely high, commercial-grade durability. The downside is…performance can vary significantly between brands, and a higher price tag is not always a predictor of performance.
It will come as no surprise that I have the utmost confidence in our recently launched EMCAT+ EC2A Topcoat, a water-based formula specifically designed to deliver commercial-grade durability on the most challenging substrates (such as oily woods).

I spent two years developing the EMCAT+ EC2A topcoat to provide true, 2K durability in as little as 24 hours, without risking your health to harmful isocyanates or aziridine 2K components.
(Note: EMCAT+ EC2A topcoat is currently available to TCPros only. EMCAT+ Si427 Sealer/Isolator is available to everyone.)
Remember that successful finishing of oily woods often requires a combination of proper preparation, appropriate product selection, and careful application techniques. When done correctly, your results can be both beautiful and long-lasting.
Do you have any experience or advice with respect to finishing oily woods? Please share your thoughts or read what others are saying in the comments section below.
Jeff Weiss is the owner and chief chemist at Target Coatings, which has been dedicated to exclusively manufacturing water-based, low-VOC and HAPs-free wood finishes for nearly 40 years. Creator of the first water-based lacquer with 100% burn-in rivaling nitrocellulose lacquer, Jeff is considered one of the “founding fathers” of water-based technology and safety for refusing to accept the “status quo” and for refusing to expose others to chemicals he wouldn’t want to be exposed to. A U.S. Air Force veteran and former volunteer EMT, Jeff has always put service and safety first. Outside of work, Jeff is an avid fly fisherman who enjoys being immersed in and inspired by Earth’s natural beauty.
We have an outdoor deck made with IPE (or similar) wood. It was installed approximately nine years ago, no sealant or stain applied. Would Si427 be a good surface – will it wear through in the traffic patterns? Wil it help restore the color tone?
Bill,
Thank you for your inquiry into our new Emcat+ Si427 Sealer & Isolator.
So far we have found that Si427 works best on “undercover” exterior applications such as under eaves and protected porch areas.
Si427 will enhance the color of Ipe, and it will provide a very good bond to it, but we are still considering it for use on fully exposed decks and horizontal surface areas that will see full UV and standing water exposures without a high-quality deck finish applied over it.
-JeffW-